limitations of hardness test|hardness testing process : trader In this article, we briefly explained the importance and application, advantages and disadvantages of Rockwell hardness test. We also introduce the Rockwell test with different . The 11" x 18" chamber gives the Ritter M11 sterilizer the distinction of being one of the largest of any standard countertop autoclaves.If an electronic malfunction is detected during a cycle, a numeric error code will appear on the display panel. Each number in the error code provides information about the problem that occurred. The table below cross-references the numeric error code with the Component, .
{plog:ftitle_list}
The word autoclave comes from the French “auto” and the Latin “clavis” and literally means self-locking—that is, the core distinguishing feature of an autoclave is that it includes a .The blowback vessel protects the feed system from unpredictable backpressure and flows. The steam/utility gases are fed into the autoclave through a blowback vessel to buffer the fluctuating pressure of the autoclave and allow response time in case of backflows. High pressure in the autoclave can push slurry into . See more
Hardness testing does have some limitations and challenges that can affect the accuracy and repeatability of hardness results, some of which are listed below: It is necessary to have properly prepared the surface of the .
In this article, we briefly explained the importance and application, advantages and disadvantages of Rockwell hardness test. We also introduce the Rockwell test with different .
Hardness testing does have some limitations and challenges that can affect the accuracy and repeatability of hardness results, some of which are listed below: It is necessary to have properly prepared the surface of the sample to .In this article, we briefly explained the importance and application, advantages and disadvantages of Rockwell hardness test. We also introduce the Rockwell test with different indenter types, such as diamond cones and carbide balls. Traditional hardness measurement is only applicable to large-sized samples, not only due to limitations of the measuring instrument, but also because the residual indentation cannot accurately reflect the true hardness of the sample at the micro- and nano-scales.There are different reasons for this: Rockwell hardness testers are usually less costly than optical hardness testers, the test itself is quick and easy, surface finish of the material is not critical, and the Rockwell scale is a commonly accepted value when purchasing products. Industrial Application. Surface Roughness.
what is a hardness test
In the manufacturing industry, we are measuring the hardness of the metal by various hardness tests and one of them is the Brinell Hardness Test. In this article, we will see its performing methods, advantages, disadvantages/limitations, and applications.
The Brinell Hardness Tester, a widely used method for assessing material hardness, offers several advantages and limitations that are important to consider when performing hardness testing. Understanding both the strengths and weaknesses of the Brinell Hardness Test is crucial for obtaining accurate and reliable hardness measurements.Hardness test methods in the macro range include Brinell, Vickers and Rockwell. Hardness testing in the low-load range applies when the test load falls between an interval of 0.2 kgf and 5 kgf (test load ≥ 0.2 kgf and < 5 kgf). The most commonly used low-load method is Vickers.
Request Quote. The Brinell hardness test is a commonly used hardness testing method that measures the hardness of materials. It does so by pressing a hard ball indenter into the surface of the material under a specified load and calculating the hardness based on the size of the indentation. Brinell hardness testing has its limitations, however, including the need to use a selection of different-sized indenters depending upon the material under test and, sometimes, it’s not suitable for testing very small components.
static hardness testing
This article describes the principal methods for macroindentation hardness testing by the Brinell, Vickers, and Rockwell methods. For each method, the test types and indenters, scale limitations, testing machines, calibration, indenter selection and geometry, load selection and impression size, testing methodology, and testing of specific .
Hardness testing does have some limitations and challenges that can affect the accuracy and repeatability of hardness results, some of which are listed below: It is necessary to have properly prepared the surface of the sample to .In this article, we briefly explained the importance and application, advantages and disadvantages of Rockwell hardness test. We also introduce the Rockwell test with different indenter types, such as diamond cones and carbide balls. Traditional hardness measurement is only applicable to large-sized samples, not only due to limitations of the measuring instrument, but also because the residual indentation cannot accurately reflect the true hardness of the sample at the micro- and nano-scales.There are different reasons for this: Rockwell hardness testers are usually less costly than optical hardness testers, the test itself is quick and easy, surface finish of the material is not critical, and the Rockwell scale is a commonly accepted value when purchasing products. Industrial Application. Surface Roughness.
industrial hardness testing
In the manufacturing industry, we are measuring the hardness of the metal by various hardness tests and one of them is the Brinell Hardness Test. In this article, we will see its performing methods, advantages, disadvantages/limitations, and applications.The Brinell Hardness Tester, a widely used method for assessing material hardness, offers several advantages and limitations that are important to consider when performing hardness testing. Understanding both the strengths and weaknesses of the Brinell Hardness Test is crucial for obtaining accurate and reliable hardness measurements.
Hardness test methods in the macro range include Brinell, Vickers and Rockwell. Hardness testing in the low-load range applies when the test load falls between an interval of 0.2 kgf and 5 kgf (test load ≥ 0.2 kgf and < 5 kgf). The most commonly used low-load method is Vickers. Request Quote. The Brinell hardness test is a commonly used hardness testing method that measures the hardness of materials. It does so by pressing a hard ball indenter into the surface of the material under a specified load and calculating the hardness based on the size of the indentation.
Brinell hardness testing has its limitations, however, including the need to use a selection of different-sized indenters depending upon the material under test and, sometimes, it’s not suitable for testing very small components.
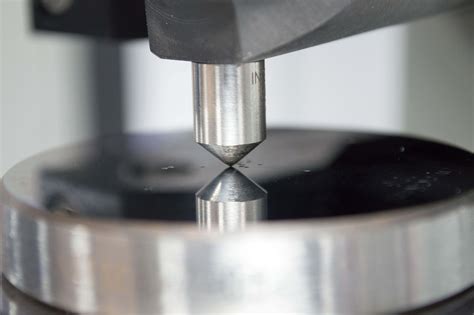
hardness testing standards explained

hardness testing scale
hardness testing process
Download PDF - Manual Sercon Ahmc [143g0e5959nj]. .
limitations of hardness test|hardness testing process